Reliable Ways to Troubleshoot Common Issues in Product Packaging Equipment Operation
In the realm of production and production, making sure the seamless procedure of product packaging equipments is extremely important to preserving effectiveness and meeting due dates. Allow's discover some efficient strategies that can assist in promptly settling common problems in product packaging equipment operation.

Identifying Common Product Packaging Equipment Issues
When fixing packaging machine issues, it is important to precisely recognize usual problems that might occur during the product packaging process. One typical issue run into in product packaging equipments is incorrect securing. This can result in products not being firmly packaged, risking damage or contamination during transport. One more constant problem is imbalance, where the product packaging materials or products are not correctly lined up, triggering jams or misfeeds. In addition, mechanical wear and tear on parts like belts, gears, or chains can lead to irregular product packaging or equipment malfunctions.
In addition, issues with sensors can disrupt the packaging process by stopping working to discover products or setting off incorrectly. packaging machine repair. Electric problems, such as malfunctioning electrical wiring or power supply issues, are also usual offenders behind packaging machine failings. Recognizing and immediately addressing these common troubles are crucial for keeping the efficiency and reliability of packaging procedures. By determining these concerns early on, drivers can avoid downtime, minimize item waste, and guarantee the smooth performance of product packaging equipment.
Carrying Out Regular Maintenance Checks
Frequently performing comprehensive maintenance checks is important for guaranteeing the optimal efficiency and longevity of packaging equipments. By sticking to an organized maintenance timetable, possible issues can be recognized and settled proactively, reducing downtime and pricey repair work. When executing regular maintenance checks, it is important to evaluate crucial parts such as belts, chains, seals, and sensing units for any type of indications of wear or damages. Lubing and cleaning up moving parts can assist stop friction-related issues and make sure smooth procedure. Furthermore, examining and calibrating settings connected to temperature, rate, and pressure can assist keep the machine's effectiveness and accuracy.
Moreover, carrying out normal inspections of electrical links and controls can assist protect against electrical malfunctions and make sure the safety of the maker operators. Documenting maintenance activities and keeping thorough documents of components replacements and repairs can aid in tracking the equipment's efficiency with time and identifying any kind of repeating concerns. Inevitably, a proactive method to regular maintenance checks is extremely important in making best use of the efficiency and reliability of product packaging makers.
Troubleshooting Electrical and Mechanical Troubles
Reliable troubleshooting of electric and mechanical problems in product packaging equipments calls for a methodical method and a deep understanding of the machine's elements and procedure. When encountering electrical problems, beginning by checking power sources, connections, and control panels for any kind of noticeable damages or loose links.
Lubrication of key components can avoid friction-related problems and make certain smooth machine operation. Verifying the alignment of components and readjusting stress where required can rectify issues connected to misalignments or irregular visit this site right here movements in the product packaging maker.
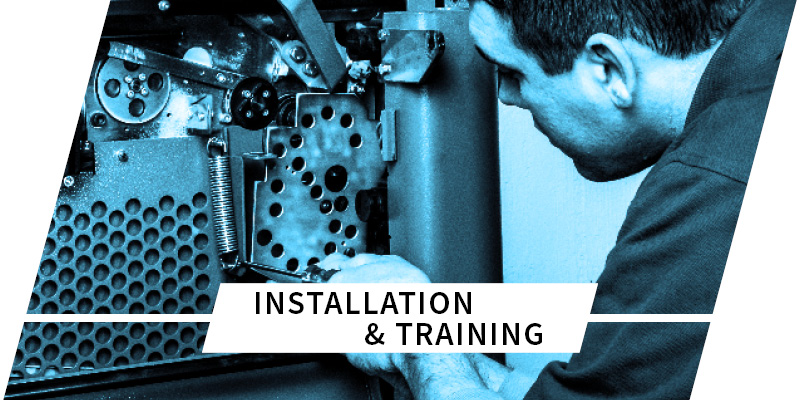
Optimizing Equipment Settings for Performance
To enhance the total performance of packaging devices, a vital aspect includes fine-tuning and enhancing maker settings for maximum performance and outcome consistency. Appropriately calibrated device setups can dramatically influence the rate, precision, and high quality of the packaging process. One crucial element to take into consideration is changing the device's speed setups to find the optimum equilibrium in between performance and precision. By fine-tuning the rate, you can prevent problems such as jams or misaligned packaging. Additionally, adjusting the pressure settings, including the sealing and cutting pressures, is critical for making certain that packages are secured safely without harming the products. Making sure the correct temperature level settings for sealing elements such as heat sealants or thermal transfer about his printers is additionally vital to preserve the honesty of the packaging. Frequently monitoring and changing these equipment settings based upon the particular demands of the product packaging materials and product can cause raised performance, minimized downtime, and improved general output quality.
Implementing Preventive Maintenance Measures
Executing preventative maintenance procedures is important for making certain the longevity and optimum efficiency of product packaging makers in commercial settings. Regular upkeep assists stop unanticipated failures, decreases downtime, and ultimately conserves time and money for businesses. To successfully apply preventative upkeep, create a comprehensive maintenance schedule detailing tasks such as cleansing, lubricating, examining, and replacing used components. This timetable must be adhered to carefully by experienced maintenance workers to guarantee that the machines operate at peak effectiveness.
In addition to set up upkeep, it is vital to keep extensive documents of all upkeep tasks carried out on the product packaging makers. These records can give valuable understandings into check it out the machines' efficiency fads, assistance recognize repeating problems, and overview future maintenance efforts - packaging machine repair. Moreover, spending in training programs for equipment drivers and maintenance team on correct upkeep procedures and methods can significantly enhance the effectiveness of precautionary upkeep steps. By focusing on precautionary upkeep, organizations can prolong the life expectancy of their product packaging devices, minimize disturbances in production, and preserve constant product quality.
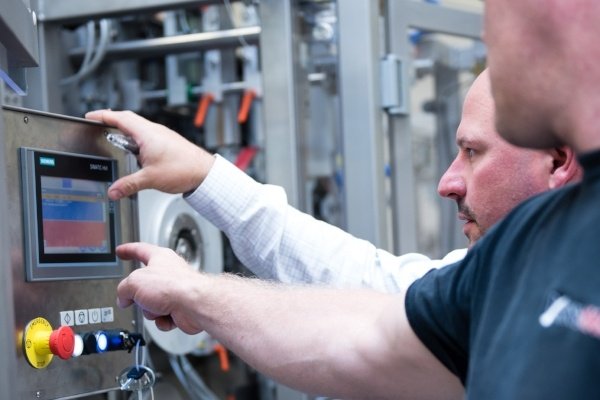
Verdict
Finally, effective troubleshooting of common concerns in packaging equipment operation entails recognizing issues, executing routine upkeep checks, repairing electric and mechanical problems, optimizing device settings for effectiveness, and implementing precautionary maintenance actions. By adhering to these actions, operators can make certain smooth and trusted operation of packaging makers, reducing downtime and taking full advantage of efficiency.
When troubleshooting product packaging device problems, it is crucial to properly identify common problems that may arise during the product packaging procedure.Reliable troubleshooting of mechanical and electrical problems in packaging devices calls for a methodical approach and a deep understanding of the equipment's parts and procedure.To enhance the general performance of product packaging makers, an important aspect involves fine-tuning and optimizing device setups for optimal effectiveness and outcome consistency.Carrying out preventive maintenance procedures is vital for ensuring the longevity and ideal efficiency of packaging equipments in industrial settings.In addition to scheduled maintenance, it is necessary to maintain thorough documents of all upkeep tasks done on the packaging equipments.